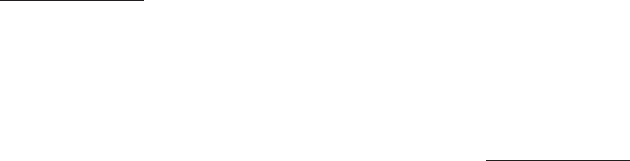
42 Wessel de Jonge
operational cost for vertical transportation of products and
workers were seen as major benets
6
. Yet, Wiebenga was
not easy on himself as, at the time, the calculation of the
omnidirectional pattern of forces around the reinforced
concrete column heads was in no way common practice
7
.
As one of the most expert reinforced concrete engi-
neers of the era, Wiebenga was so up-to-date about new
developments in his eld that he was often successful in
challenging the building inspectorate and ruling stand-
ards. He was annoyed by the limitations that were im-
posed by such regulations: One moves the buoys with the
tide […] it is now more than time to break with the system
to establish simple rules, that may appear understandable
also to non-experts […] New regulations must be edited
in such a way that only experts can understand them and
(they) should be limited to the denition of standards that
dene the relationship between design, calculation, per-
missible stresses and material qualities [11, pp. 188, 189].
As a civil engineer, on the other hand, Wiebenga was
pragmatic and he repeatedly proposed heavier construc-
tions if he expected those to be more economic in terms
of construction time or cheaper materials
8
. Duiker on the
other hand, departed from the theoretical concept of “spi-
ritual economy”, in which the use of materials was to be
economized.
Calculation
The introduction of reinforced concrete for architectur-
al purposes in the Netherlands was around 1900. In 1912
the rst Reinforced Concrete Codes were published after
a German example of 1903, followed by a new edition in
1918. Some of the assumptions about concrete technolo-
gy deviate signicantly from those on which present day
regulations are based.
For instance, one was not aware of the eect of the
alkalinity of cement and its role in protecting the rein-
forcement against corrosion. The devastating eects of
curing-agents like calcium chlorides were unknown. The
relationship between water-cement ratio and compression
strength was known, but the connection with porosity was
not recognised. Today this is a main source of failure as
a result of carbonation due to high CO
2
levels caused by
air pollution.
6
Remarkably, Van der Vlugt used the mushroom oor system him-
self already in 1924 in a Rotterdam warehouse but for the Van Nelle facto-
ry the architects initially would not give up their proposal for a beam struc-
ture. The client eventually preferred Wiebenga’s proposal partly because
of these advantages for the company’s business operations [9, p. 61].
7
The mushroom oor system was patented by the American C. Tur-
ner in 1906. The rst known European example is an experimental struc-
ture patented by R. Maillart in 1908, and his design for the Giesshübel
department store in Zürich of 1910. The initial complex pattern of rein-
forcement nets was simplied around 1910 by the introduction of a sin-
gle orthogonal reinforcement net, which eased calculations [9, p. 61]. At
the Van Nelle Factory, the orthogonal reinforcement around the column
heads was placed diagonally, as can be seen on photographs that were
made during construction [10, pp. 107, 113].
8
Such arguments are mentioned in footnote 17, as part of the dis-
cussion about the choice for a beam structure or ush oor slabs for the
Van Nelle factory [9, pp. 59–61].
The reinforced concrete constructions that were de-
signed with primary and secondary beams were calculated
as beams on two supports
9
. The reinforcements to mush-
room columns were placed orthogonally and, similarly to
beam structures, were calculated accordingly. Although
one acknowledged that monolithic concrete constructions
are statically indenite and the theory of elasticity applied,
one was not yet fully aware of how to take full advantage
of this knowledge. As a result, for security reasons, lower
material stresses were accepted than would be used today.
This, of course, contrasts with the principle of the economic
use of materials that was embraced by the architects of the
Modern Movement – one may say that the slender struc-
tural frame of sanatorium “Zonnestraal” is a true miracle.
Progressive collapse was not taken into account, while
today we would rather take the collapse of the building as
a whole as a reference
10
. Finally, expansion joints were
not required, though sometimes still made
11
.
Execution
When it comes to the execution of the works generally
we see that the lack of experience and sophistication of
equipment on site were not helpful to the quality of early
architectural concrete [10, particularly: pp. 90, 97–109].
In particular mixing concrete by hand did not result in
a homogeneous mortar so that the quality of such concrete
often shows great variety. This was often worsened by the
use of wheelbarrows for onsite transportation and the con-
sequent load by load pouring of the slurry (Fig. 5).
Due to the slender dimensions it appeared sometimes
dicult to t the reinforcement into the form work,
leaving the steel often too close to the surface resulting
in a lack of cover of the reinforcement steel. It was not
unusual to mix the mortars with additional water to ll
the narrow form works. As a result, the concrete is of-
ten porous, with a great variety in compression strength
and showing gravel pockets. The plaster on the concrete
surfaces unintentionally provided some protection to the
reinforcement due to it is alkaline character. At the same
time it concealed the irregularities of the concrete surface.
It was only after the World War II that the use of exposed
reinforced concrete become more mainstream.
Inside or out
At the sanatorium, Duiker made use of the cantilever-
ing roofs as canopies in order to allow the curing patients
to sit outdoors but protected from the direct sunlight. The
steel fronts of the façades have therefore been set back,
9
As early as 1886 Hennebique argued that tensile forces in rein-
forced concrete should be absorbed entirely by the reinforcement steel,
and that the reinforcement should therefore not be evenly distributed
but mainly be placed where these forces occur, i.e., at the bottom (in the
middle of the beams) and at the top (where the beams are supported).
10
For example Vermaas [12] and Wattjes [13].
11
At the sanatorium, dilatations are completely absent, but at the
much longer structures of the Van Nelle factory, expansion joints have
been provided.